Highlights
Two-stage dry-running KOTECH air rotary screw compressors not only impress with their meticulous design, but also with their many innovative details are based on the KOTECH air quality.
🔧 German-Made Air End
Equipped with high-quality oil-free GHH air end from Germany for outstanding durability and performance.
🔇 Clean & Quiet Operation
Zero oil, low noise, and long service life ensure a clean and eco-friendly compression process.
💸 Low Maintenance
Requires minimal servicing, helping reduce running costs over time.
🏭 Versatile Applications
Ideal for food, medical, electronics, and any industries needing oil-free air.
📦 Compact Design
Space-saving layout fits easily into limited or tight installation areas.
💨 Pure & Dry Air
Delivers clean, moisture-free air for sensitive and critical operations.
🚀 Innovation You Can Trust
Designed by KOTECH engineers for top performance and efficiency, with power options up to 350 kW.
🛠️ Service-Friendly Design
Easy access to components, large maintenance doors, and swing-out cooler make servicing quick and simple.
Technology
Reliable Airends
At the heart of every air dry-running rotary screw compressor lies a tried and tested dry-running two-stage rotary screw airend.
Providing optimum performance and dependability, every airend ensures maximum efficiency throughout its entire service life.
Heat Resistance
The blasted and bonderised rotors are treated using the special “Ultra Coat” process to produce an innovative and durable coating which is resistant to temperatures of up to 300 °C.
Because this cost-reducing coating is highly abrasion-resistant, its sealing and protection performance remains consistent even after years of operation.
Chromium Steel Rotors
The second compression stage’s rotors are made from stainless steel, which eliminates the risk of rotor seizing or jamming caused by corrosion.
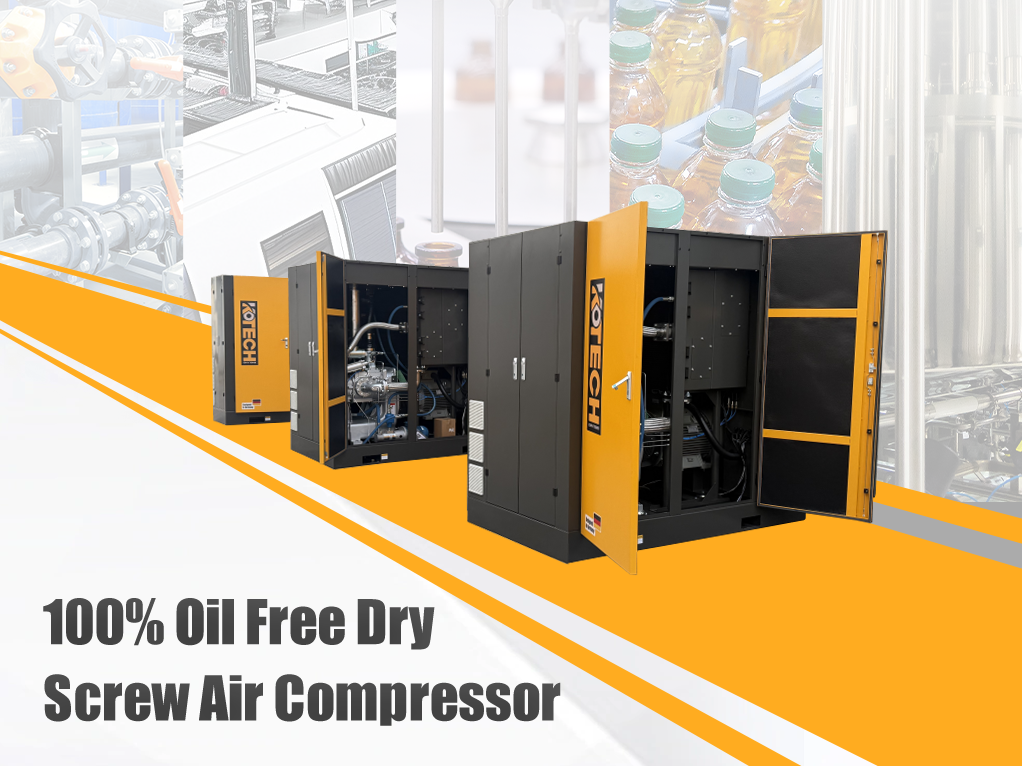
Airend Cooling
ln the places where things really needs cooling, i.e. in the second compression stage, coolant flows directly through the walls of the airend housing to ensure best possible heat dissipation and compression efficiency.
Equipment
Complete Unit
Oil-free compression rotary screw compressor with two-stage compression; condensate separator, condensate drain and fibre-free pulse dampers for both compression stages; oil tank ventilation with micro-filter,ready for operation, fully automatic, silenced.
Drive Motor
Siemens drive motor, quality manufacture; IP 55 enclosure protection, Pt100 temperature sensor in windings; continuous measurement and monitoring of motor windings temperature.
Oil-free Airend
Two-stage, oil-free compression rotary screw airend with integrated gearing and collection tank for gear oil. Rotors feature durable coating. Both high and low pressure compression stages feature jacket cooling; high pressure two-stage with chromium steel rotors.
Kotech oil free dry air compressor installation site
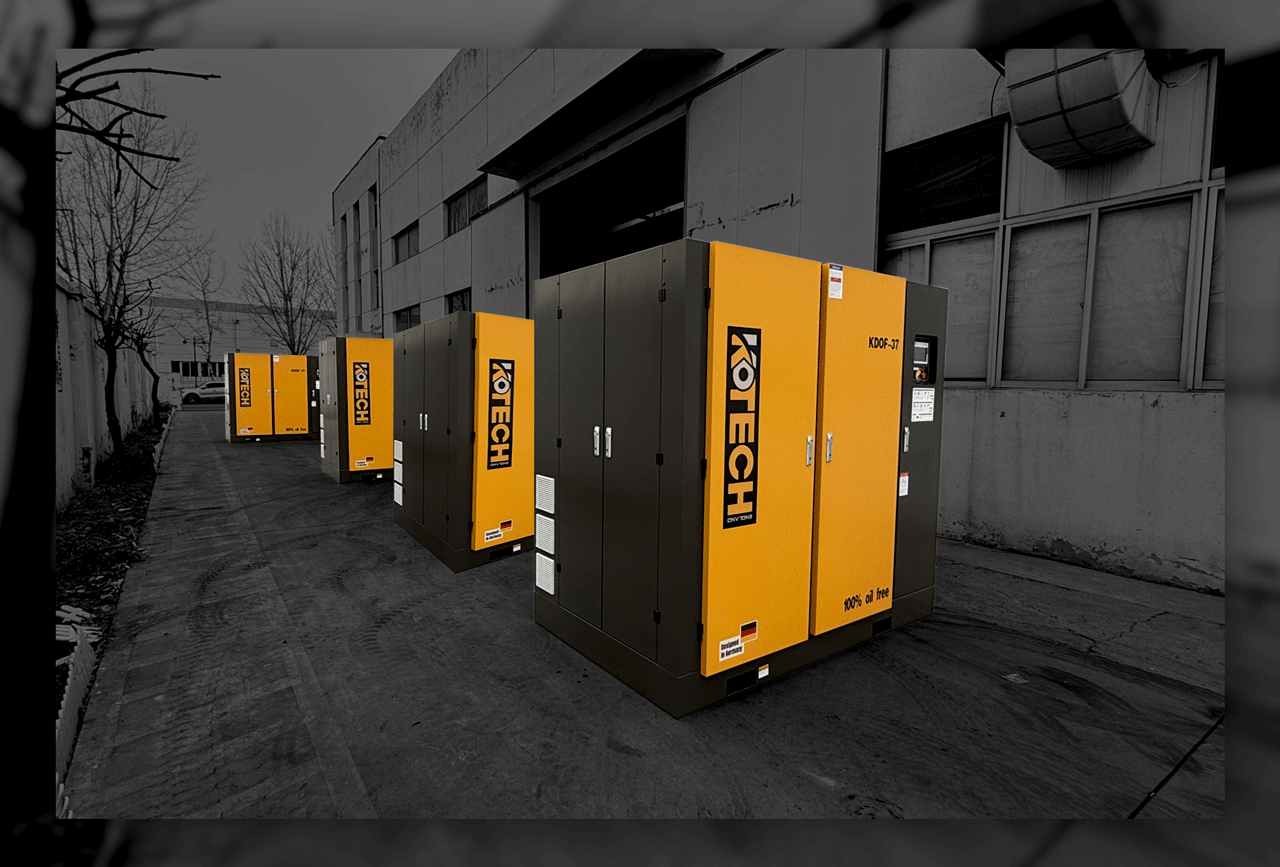
(KDOF-37 series 100% oil free dry screw air compressors)
Cooling
Optionally available with air- or water-cooling. Radial fan with separate drive motor.Exhaust air discharged up-wards.
- Air-cooled version:
High-pressure side: aluminium cooler with stainless steel tube pre-cooler. Low pressure side: aluminium cooler; aluminium cooler for gear oil.
- Water-cooled version:
Two shell and tube heat exchangers including: coated steel sleeves and pipes made of CuNi10Fe; a gear oil cooler.
Electrical Components
Ventilated lP 54 control cabinet, automatic star-delta starter, overload relay, control transformer.