Sustainable Development
Innovation-driven, sharing a green future. Together with you, forging the path to sustainability.
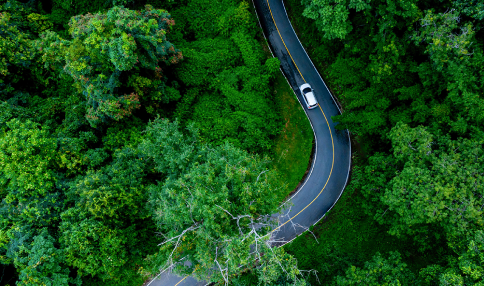
Collaboration Process
Inquiry > Study the client background > Negotiation > Order(deposit) > Confirm production order > Manufacturing > Finish production > Loading(balance) > Transportation > Customs clearance > (PL&CL) Receiving > Operation > Keep in touch with customers
Delivery Instructions
Step 1: Requirements Gathering
Before the start of the production order, it is necessary to fully communicate with the customers to understand the final demands and requirements. This includes product specifications, quantity, delivery time, quality standards, etc. At the same time, it is also necessary to understand the customer’s industry background, competitor situation, market demand, etc., in order to better provide customers with customized solutions.
Step 2: Scheme Design
Based on customer’s requirements, we design solutions that fit customer needs. During the planning process, it is necessary to consider the function, performance, appearance and other aspects of the product, and conduct adequate timely communication and confirmation with customers to ensure that the plan can meet customer expectations.
Step 3: Manufacturing
Once the design is confirmed by the customer, it can enter the production and manufacturing stage. At this stage, a detailed production plan needs to be developed to ensure that the product can be delivered on time. At the same time, it is necessary to purchase and deploy necessary parts, organize the production process, and perform product assembly, processing, debugging and other operations.
Step 4: Quality Inspection
During the manufacturing process, strict quality inspection is required to ensure that the products can meet customer quality standards and requirements. Quality inspection includes inspection of raw materials, monitoring of production processes, and testing of finished products, sampling inspection, etc. If quality problems are found, corrective measures need to be taken promptly to ensure the quality of the product.
Step 5: Product delivery
After the production is completed, the product needs to be delivered to the customer according to the agreed time. During the delivery process, the product needs to be packaged, shipped, transported and other operations to ensure that the product is not damaged during transportation. At the same time, it is also necessary to communicate with customers and arrange delivery details to ensure that products can reach customers on time.
Payment Terms
Payment methods include T/T, L/C, Western Union, and Credit Cards, in USD, RMB, Euro, etc. For T/T, pay 30%/50% upfront and the rest before loading. L/C must be 100% confirmed, payable at sight.
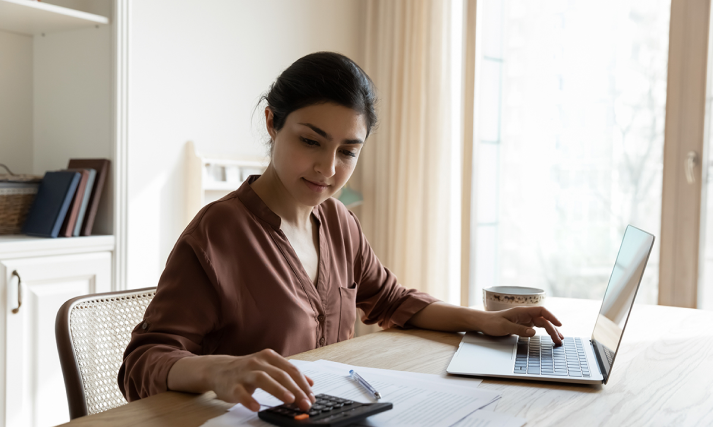
Afer-sales Warranty Service
One year for the whole machine except consumble spare parts. After the product is delivered, after-sales service is also required. After-sales services include product installation and testing, training, etc., to help customers use products correctly and solve problems that arise. At the same time, we also track customer usage, promptly solve customer problems and needs, and provide satisfactory services. The above are the main steps of the engineering order production delivery project process. Through careful execution and control of each step, we can ensure that products can be delivered to customers on time and according to quality requirements, improve customer satisfaction, and promote the development and growth of the enterprise.